SOLUBILITA’
DELL’ IDROGENO
Solubilità
nell’alluminio puro
L’idrogeno
e’ l’unico gas con una rilevante solubilità
nell’alluminio fuso. Sfortunatamente e’ facilmente
solubile e abbondante, con il risultato che
tutto l’alluminio fuso contiene una fastidiosa quantità
d’idrogeno.
Questo gas gioca il ruolo principale
nello sviluppo dei difetti dovuti alla porosità dei
getti e del considerevole sforzo nel controllare
la sua presenza e la conseguente necessità di
rimuoverlo.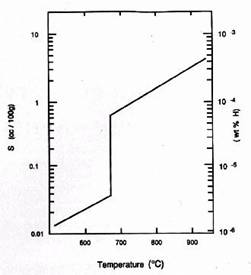
La natura del problema idrogeno
nell’alluminio, e’ molto evidente nella FIGURA 1, dove si vede che la solubilità dell’idrogeno ha
tre distinte caratteristiche:
-
Una
forte dipendenza dalla temperatura
nello stato liquido, implicando che l’aumento
di temperatura aumenta l’idrogeno, infatti, la
solubilità dell’idrogeno raddoppia ogni
110* C di aumento di temperatura.
-
Bassa
solubilità nell’alluminio solido.
-
Grande
variazione della solubilità in
corrispondenza del punto di fusione.
Questi due
ultimi fattori dimostrano che la grande quantità d’idrogeno presente nel liquido non
riesce a dissolversi durante la solidificazione e raffreddamento. L’idrogeno accumulato nel
liquido causa la formazione di porosità.
Solubilità
nelle leghe d’alluminio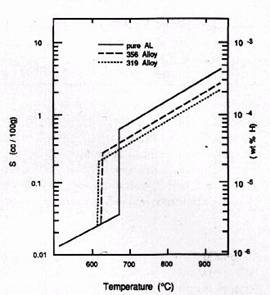
L’aggiunta
di elementi nell’alluminio cambia la solubilità
dell’idrogeno. Alcuni elementi come il silicio, zinco, rame e manganese diminuiscono la solubilità, così
come magnesio, titanio, nichel e litio la incrementano
Nella
FIGURA 2 vediamo la solubilità per le leghe 356 e 319.
Sorgente d’idrogeno
La maggior
parte d’idrogeno presente nell’alluminio,
deriva dalla reazione del vapore acqueo sulla
superficie dell’alluminio secondo la reazione:
2Al + 3H2O
----> Al2O3
+ 6H
Questa
reazione e’ molto presente alle temperature
operative di fonderia ed evidenzia che tutto il vapore acqueo
che viene in contatto con l’alluminio liquido partecipa a questa
reazione. Lo strato di ossido (pelle) che si forma sopra i bagni
protegge in parte da questa reazione. E’ importante notare che,
intorno a 930* C il film di ossido perde la sua natura
protettiva e il vapore acqueo può penetrare fino al metallo
sottostante. Sebbene questa temperatura sia lontana dalle
normali temperature di fusione, sarà importante evitare che,
alcune zone della superficie raggiungano questi valori (per
esempio durante la fusione).
L’Atmosfera
L’atmosfera
e’ una delle più importanti fonti di vapore acqueo. Per esempio
l’aria a 26* C e 65 % di umidità relativa, contiene almeno 16
g/m3 di acqua.
Flussi
I flussi di
fonderia sono sali igroscopici che assorbono acqua
dall’atmosfera. Aggiunti al metallo, causano un notevole
incremento di gas. I flussi dovranno essere stoccati in
sicurezza e preriscaldati a circa 100* C per evitare che
assorbano acqua. Questi riassorbono acqua, pertanto dovranno
essere usati subito dopo il preriscaldo. Alcuni flussi
contengono acqua di cristallizzazione contenuta all’interno dei
propri cristalli. In questo caso e’ molto più difficile
rimuovere l’umidità’ e si arriva a riscaldarli a 200* C e oltre.
Crogioli
I crogioli
nuovi contengono sempre umidità. L’alluminio fuso in un crogiolo
nuovo, e’ sempre più gasato di quello fuso in un crogiolo
vecchio. Si raccomanda, infatti, un adeguato preriscaldo.
Combustibile
Il prodotto
della combustione contiene da 10 % a 20 % di vapore acqueo. Il
gas naturale produce più di 2 m3 di vapore acqueo per ogni metro
cubo di gas bruciato. Per ridurre l’idrogeno sviluppato da
questa sorgente, si raccomanda una regolazione della fiamma
leggermente ossidante.
Refrattari
Come i
crogioli, i refrattari nuovi contengono umidità.
Attrezzi
di fonderia
Gli
attrezzi in genere come canali tazze se non sufficientemente
preriscaldati, sono un’importante fonte d’idrogeno.
Un metodo
per calcolare indirettamente il livello d’idrogeno e’ dato dalla
seguente formula:
ml H2/100
g di Al = 100 (1/Ds
– 1/Dt)
dove Ds
=
densità del campione
Dt
=
densità teorica della lega
Ds
=
colare un campione e calcolare la densità mediante il principio
di Archimede.
Dt
=
calcolare la densità matematicamente utilizzando l’analisi
chimica della lega, oppure misurare la densità con lo stesso
principio di Archimede dopo un perfetto degasaggio.
|